The injection molding process may seem simple, but it is not. The injection molding process has strict requirements on mold temperature and pressure, operation and equipment. A little carelessness will cause problems in the appearance and structure of the plastic parts, and a series of difficult conditions such as discoloration bubbles will occur. Today, the editor summarized the process problems that Shenzhen injection molding factory often encountered in the production process, and hope to help everyone.
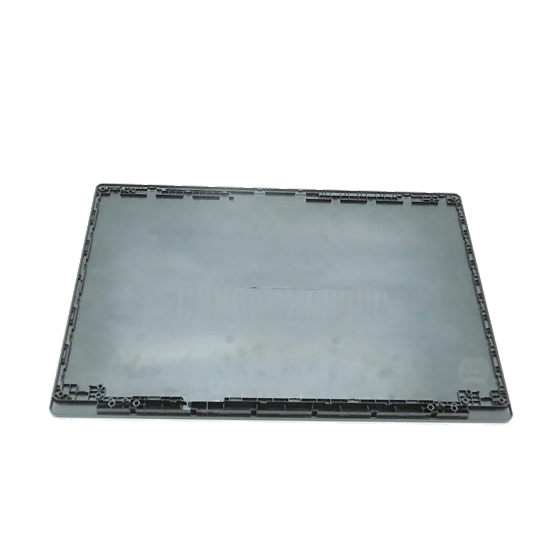
1. Insufficient product injection
Insufficient product injection is often due to the fact that the material has solidified before filling the cavity. Of course, there are many other reasons. The main reasons for the equipment are: the hopper is interrupted; the neck of the hopper is partially or completely blocked; the feeding amount is not enough or the feeding control system is not operating normally; the plasticizing capacity of the injection press is too small and the injection cycle is abnormal due to the equipment. The injection pressure is too low; the injection pressure loss during the injection cycle is too large; the injection time is too short and the total pressure time is too short; the injection rate is too slow, etc.
2. Flashing material
Product overflow is often caused by the defects of the mold. Other reasons are that the injection force is greater than the clamping force. The temperature of the material is too high, the exhaust is insufficient, and the mold is overfilled with foreign objects. Mold problems: The cavity and core are not tightly closed, the cavity and core are offset, the template is not parallel, the template is deformed, and the amount of square meters you fall into the foreign body, and the exhaust is insufficient. Equipment problem: The projected area of the product exceeds the injection area of the injection press, the injection press template is installed incorrectly, and the injection cycle caused by the equipment is abnormal.
3. Product dents and pores
Product dents are usually due to insufficient force on the product, insufficient material filling and unreasonable product design. The dents often appear in the thick-walled part close to the thin wall. To determine the cause of the pores, it is only necessary to observe whether the bubbles of the plastic product appear instantaneously when the mold is opened or after cooling. If it appears instantaneously when the mold is opened, it is mostly a material problem, if it occurs after cooling, it is a problem with the mold or injection molding conditions.
Temperature is a very important process parameter in Shenzhen injection molding plant. Improper temperature will cause various process problems. Too hot materials cause excessive shrinkage and too cold materials will cause insufficient filling and compaction; in addition, the temperature of the mold is also very important. Too high mold temperature causes the material at the mold wall to not solidify quickly and the mold temperature is too low. Insufficient mold filling and excessively high mold temperature can also cause various problems.