The hot runner system is a very versatile plastic molding and pouring system. The heating device and the electronic temperature control system are mainly used to prevent the molten plastic in the pouring system from solidifying, so that the plastic is filled into the mold cavity smoothly and orderly. In the absence of injection pressure. The molten plastic will not flow automatically, nor will it cause wire drawing or overflow with the demolding of the plastic product. Therefore, the hot runner mold is also called the no-flow mold or the less-runner mold.
For a long time, the injection molding system of plastic molds has always used cold runners to inject molten plastic into the mold cavity. With the advancement of science and the continuous development of productivity, people have begun to realize many disadvantages of traditional injection molds, including hot runner waste. The production and use of the = longer molding cycle and low production efficiency, which directly leads to an increase in cost.
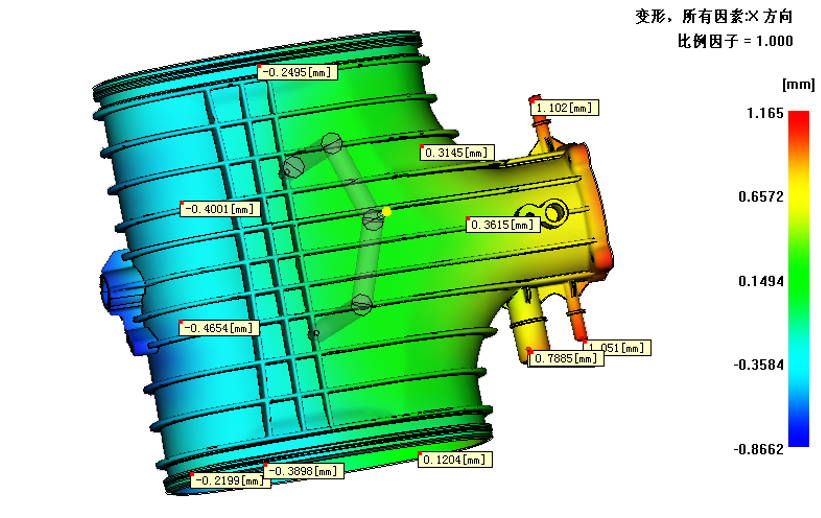
With the emergence of 3D software, the structure of plastic products is becoming more and more complex, and the requirements are getting higher and higher. Therefore, traditional molds have been unable to meet the needs of modern products in terms of molding processes, and people have to consider other technical processes. The American Lncoe company invented the hot runner injection molding mold technology, which set off a revolution in the mold industry. Especially in recent years, with the development of microelectronics technology and the invention of electronic temperature control boxes, the hot runner system has developed to a very mature stage.
Comparison of the advantages of hot runner and cold runner
A cold runner
1. During the injection molding filling process, due to the continuous loss of heat at the front end of the material flow, the surface of the material flow is solidified, and the injection pressure loss is large, which directly affects the service life of the injection molding machine.
2. During the injection and filling process, due to the continuous loss of heat at the front end of the material flow, the surface of the material flow is solidified, resulting in an even temperature step of the plastic injected into the mold. It may directly lead to a series of problems such as printing, welding marks, deformation, warpage, depression, and dissatisfaction of the plastic products after molding, which makes the plastic products unable to meet the requirements.
3. Due to the production of cold runners, factories need to design special waste secondary processing equipment, resulting in waste of manpower, material resources, and materials.
4. The mold has a long cooling time and a long filling time, resulting in low production efficiency.
Two hot runner
1. The heated temperature of the hot runner is almost the same as the temperature of the barrel and nozzle of the injection molding machine, which avoids the phenomenon of condensation of molten plastic on the inner surface of the runner, and the injection pressure loss is small.
2. After the plastic is molded, the quality is high, because the temperature, pressure and density of the plastic after being injected into the cavity are uniform, the internal stress of the plastic part after molding is small, the deformation is also small, and the size is stable.
3. No waste, save materials, save resources and costs.
4. The mold cools quickly, fills quickly, the molding cycle is short, and the production efficiency is high.
Disadvantages of hot runner modeling
1. Because the heating runner system has a heating mechanism and a manifold mechanism, it takes up a lot of space. Therefore, the overall height of the mold needs to be increased, which directly leads to an increase in mold cost.
2. The heat loss is serious and difficult to control
3. Severe thermal expansion will occur after heating
4. The hot runner system is expensive, leading to increased mold manufacturing costs.
Features of hot runner modeling
1. The melting temperature range of plastics is relatively wide, at low temperatures. Good fluidity and good thermal stability at high temperature.
2. Sensitive to pressure, no flow without pressure, but can flow after applying pressure.
3. Good thermal conductivity, fast heating and fast cooling.
Several issues that need attention in hot runner modeling
1. Due to severe thermal expansion after heating, there must be enough space between the hot runner system and the mold for expansion
2. Large-area contact between the hot runner system and the mold should be avoided as much as possible.
3. Because of the serious heat loss, a heat insulation pad should be added between the mold and the injection molding machine to reduce heat loss. The heat insulation board must have insulating materials. Commonly used are bakelite, various plastic sheets and glass fibers.