The hot runner system is mainly composed of four parts: main temperature controller, sprue sleeve, manifold and hot nozzle. According to the type of glue feeding, it can be divided into two types: single-point type and multi-point type. The single-point type has only one nozzle and one glue inlet point. For some round products with higher requirements, sometimes one nozzle has multiple glue inlet points. Multi-point type has multiple nozzles and multiple injection points. The single-point type generally does not require a manifold. Some molds are limited by the shape of the product, and the position of the glue port needs to be far away from the center of the mold. Sometimes it is necessary to increase the size of the mold or the tonnage of the injection molding machine. This will directly lead to an increase in the overall cost. For this reason, the single nozzle hot runner needs to add a manifold, and the mold does not need to be eccentric. The multi-point type must use a manifold. The hot nozzles of the hot runner are commonly used large nozzle type, point gate type, pneumatic needle valve type and so on.
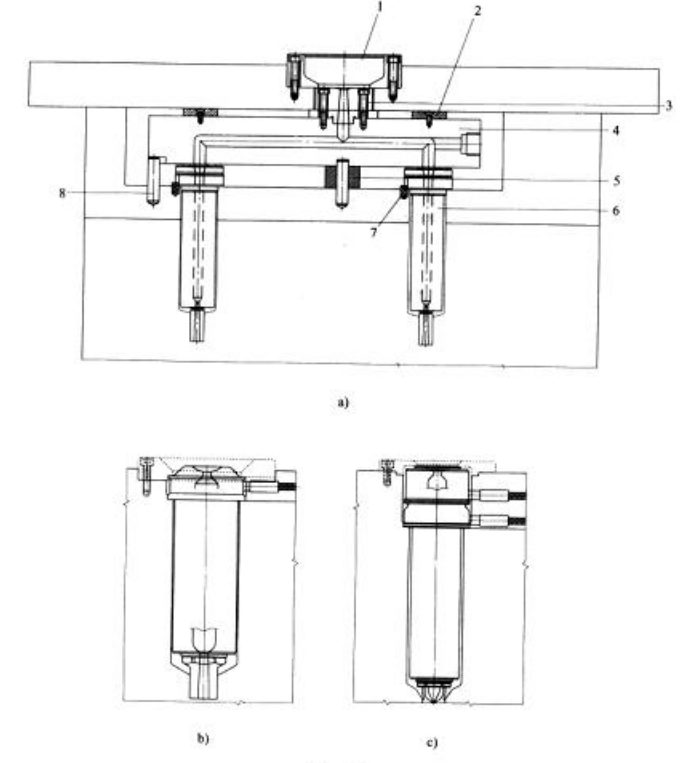
Figure 1-2a is a commonly used multi-point open hot runner system. It is usually used on a large mold with one cavity and one cavity or a mold with multiple cavity. When the product is too large, multiple gates and multiple gates are needed. When the distance between them is too far, this form must be used. Another feature of the hot runner is that it can not only feed the glue directly on the surface of the product, but also turn it into a cold runner to feed glue, which is usually said to be a hot runner to a cold runner. However, this kind of open hot nozzle is mostly used in molds that convert hot runners to cold runners. When a mold has multiple cavities, it is sometimes necessary to use this form in order to reduce the length of the cold runner. This kind of hot nozzle is of the large nozzle type, and the front end of the hot nozzle can be processed twice, and can be processed into a curved surface, an inclined surface, or a runner, etc., as required. Figure 1-2b shows a commonly used single-point open hot runner system. It has no splitter plate and only a hot nozzle. It is mostly used in a mold with multiple cavities and short runners from hot runner to cold runner. Sometimes it can also be used. Directly inject glue on the surface of some products that are not demanding. The disadvantage of this open hot nozzle is that it will leave a piece of waste. For example, direct glue on the surface of the product requires a secondary trimming of the glue port. The hot nozzle is used in many steps. Figure 1-2c is also a commonly used single-point open hot runner, which is basically used on the mold for direct product surface injection. Compared with the previous two, its advantage is that there is no waste, no need to trim the secondary gate, and the production efficiency is higher. This kind of hot nozzle can not only be used with a single nozzle. It can also be used on the mold of the multi-point hot runner system. It is an ideal choice for large products that need to be glued directly on the surface. The disadvantage is that a circle and a dot are left on the surface of the product. Therefore, it cannot be used on product molds that require higher appearance.
In addition to the above-mentioned common structures, the hot runner system also has many other structure types, because different hot runner manufacturers have different standards. You only need to fundamentally understand the principle and method of use of the hot runner. As for its internal structure and theoretical knowledge, there is no need to spend too much time to study it. I will not list them all here.